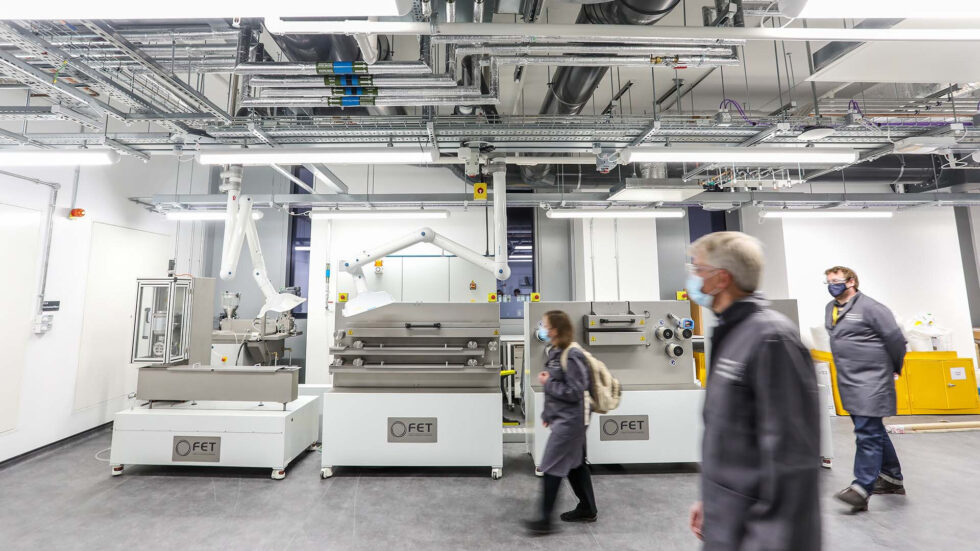
La producción de fibra de carbono es fundamental para diversas industrias, como la aeronáutica y la automotriz, debido a sus propiedades de resistencia y ligereza. Sin embargo, los métodos tradicionales de producción de esta fibra dependen de materiales costosos y derivados del petróleo, lo que incrementa tanto los costes como el impacto ambiental de su fabricación.
En este contexto, el lignina, un subproducto común de la producción de celulosa, se presenta como una alternativa sostenible prometedora. Cada año, se generan aproximadamente 70 millones de toneladas de lignina, que a menudo se considera un residuo o se quema para generar energía, dejando su potencial para aplicaciones de alto valor, como la fabricación de fibra de carbono de nueva generación, sin explotar.
Innovaciones en la producción de fibra de carbono
La empresa Lixea ha colaborado anteriormente con el Imperial College de Londres para desarrollar una tecnología patentada que permite convertir lignina en fibra de carbono a pequeña escala. Este proceso se basa en dos innovaciones clave:
- Tecnología de líquidos iónicos: disolviendo diferentes tipos de lignina y permitiendo que el líquido se recicle tras la formación de la fibra.
- Poli(vinilo)alcohol (PVA): un polímero biodegradable y no tóxico que se utiliza como ayuda para el hilado.
Esta metodología no solo posibilita la producción de fibras con un alto contenido de lignina (75%–90%) y una excelente estructura y rendimiento, sino que también reduce significativamente los costes. Al sustituir los precursores derivados del petróleo por lignina y líquidos iónicos, ambos materiales renovables y menos tóxicos, se podría reducir el coste de producción entre tres y cinco veces.
Investigadores de la Universidad de Manchester, liderados por el profesor Jonny Blaker, han llevado a cabo una demostración a escala piloto en la Plataforma de Tecnología de Fibras del Instituto Henry Royce. Se utilizó lignina procedente de la planta piloto de Lixea, que extrae lignina de residuos de madera, garantizando la alineación del proceso con las tecnologías existentes de la empresa.
El equipo de Manchester evaluó tres tipos de lignina: dos derivadas de aserrín de abeto y una de bagazo, un subproducto de la producción de azúcar. Sorprendentemente, la lignina obtenida del bagazo resultó ser la más efectiva, permitiendo por primera vez el hilado continuo de fibra a escala piloto.
Desafíos y avances futuros
Durante las pruebas, surgieron varias lecciones críticas. En primer lugar, el control del secado fue fundamental para evitar la contracción de las fibras. En segundo lugar, las soluciones de lignina se volvieron más viscosas con el tiempo, lo que exigió ajustes constantes para mantener la calidad. Por último, el diseño del hilado afectó la uniformidad de la fibra, lo que destacó la necesidad de una mayor refinación en este aspecto.
A través del proyecto, el equipo logró producir fibras continuas de hasta 5 metros de longitud. Los siguientes pasos incluyen la optimización de los procesos de secado, recolección y carbonización de las fibras, elementos esenciales para escalar esta tecnología innovadora en el Reino Unido.
El éxito de Manchester en la escalabilidad de esta nueva tecnología representa un avance significativo hacia la producción comercial viable de fibra de carbono sostenible. «Estamos entusiasmados de demostrar el potencial de escalado de este proceso pionero para crear una alternativa renovable y de bajo coste a la fabricación convencional», comenta el profesor Blaker.
Con la colaboración continua de la industria y el avance en la tecnología, la fibra de carbono basada en lignina podría convertirse pronto en una alternativa comercial escalable, de alto rendimiento y respetuosa con el medio ambiente frente a los materiales derivados del petróleo. El papel pionero de Manchester en la escalabilidad de esta tecnología refuerza su posición como líder en innovación de materiales y fabricación sostenible.